A company’s workplace environment plays a significant role in determining industrial efficiency. Everything from lighting and noise levels to safety practices and ergonomic design affects how productive and successful operations can be.
Optimizing various aspects of the work setting means manufacturers can improve employee performance, reduce errors and waste, and gain a competitive advantage.
Provide Proper Lighting
Sufficient lighting is essential for workers to perform duties safely and accurately. Production areas should have a uniform, glare-free light focused on work zones. Brightness levels should be appropriate for the detailed nature of tasks without causing eye strain.
Regular cleaning of light covers maintains optimal illumination. Position lights so they do not cast shadows on workspaces or create blinding reflections. Streamline shapes, colors, and luminance to minimize visual fatigue.
Emergency backup lighting must be activated promptly during outages to prevent disruptions. Natural daylight can supplement artificial lighting and boost morale if glare and heat are controlled.
Control Ambient Noise
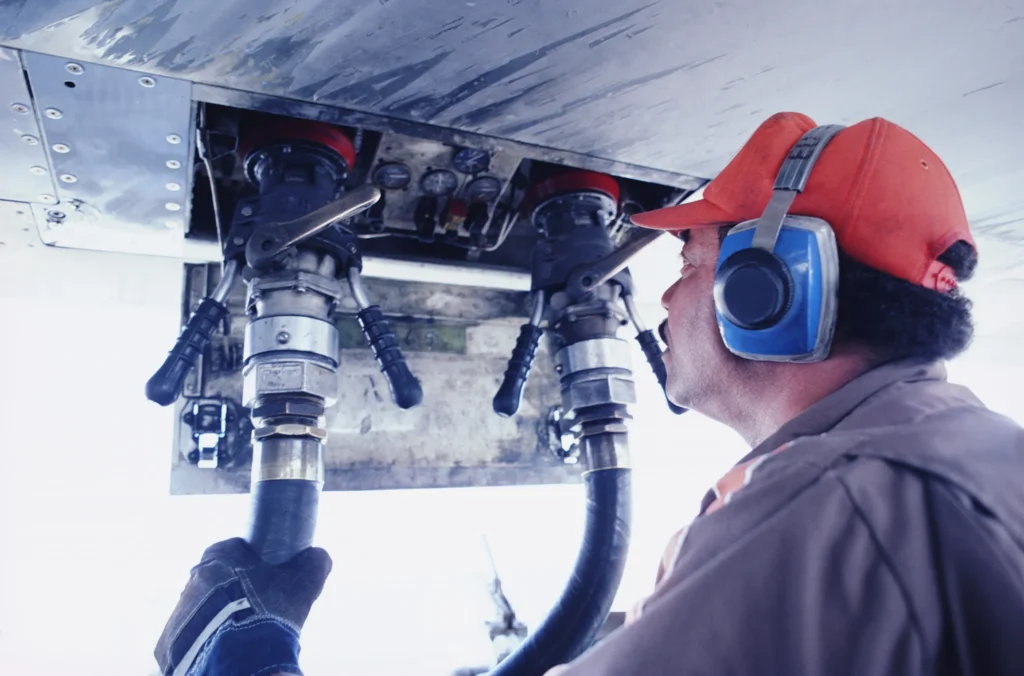
Excessive ambient noise from machinery, vehicles, alarms, and other sources can impair communication, focus, and job accuracy. Perform facility-wide noise level assessments to identify problem areas.
Enclose or isolate especially loud equipment to dampen reverberation. Install noise absorption materials on walls, ceilings, and machinery covers. Maintain equipment to prevent rattling, squeaking, and grinding noises. Replace worn or unbalanced machine parts that vibrate or hum.
Use earplugs, earmuffs, and noise-cancellation headsets to protect workers’ hearing. Limit radio use and unnecessary chatter on the production floor. Create designated quiet zones for tasks requiring concentration, inspection, or testing.
Keeping background noise from exceeding hazardous levels preserves work quality, morale, and hearing health.
Prioritize Air Quality
Air quality directly affects workers’ respiratory health and stamina for labor-intensive jobs. Identify any airborne particulates, fumes, gases, or toxins present. Control particles by enclosing processes, improving ventilation, and using HEPA air filters.
Install fume extractors and local exhaust systems to capture emissions at their source before they spread. Monitor air quality regularly to confirm levels are below permissible exposure limits. Choose cleaning products and paints with low VOCs to minimize irritating vapors. Prohibit smoking indoors to prevent secondhand smoke risks.
Keep relative humidity between 40 and 60 percent to inhibit mold growth while avoiding overly dry air. Good indoor air quality keeps staff healthy, energetic, and breathing comfortably.
Design Ergonomic Workstations
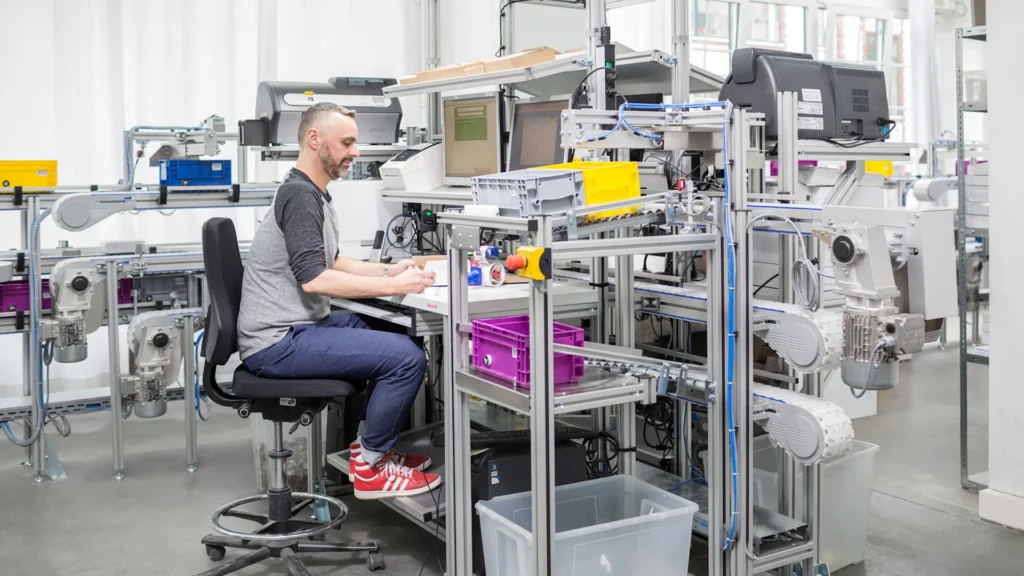
Preventing repetitive strain injuries requires designing workstations and tasks to fit employees’ bodies and abilities. Provide adjustable chairs, worktables, lifts, and platforms to accommodate individual sizes and capabilities. Position frequently used tools and materials within easy reach.
Adjust work heights so tasks can be performed without excessive bending or stretching. Provide wrist supports and padded floor mats for standing tasks. Rotate workers through different ergonomic stations to vary movements and postures. Allow regular breaks to stretch muscles and improve circulation.
Train workers on proper lifting methods and provide dollies or carts for moving heavy loads. Ergonomic workspaces lessen fatigue while preventing long-term problems like carpal tunnel or back pain.
Emphasize Safety Precautions
No efficiency gains are worth risking workers’ health and safety. All equipment must have proper machine guarding and emergency cut-off switches. Ensure mandatory health and safety law posters are displayed prominently.
Keep aisles and exits clear of obstructions for emergency evacuation. Provide appropriate personal protective equipment (PPE) and enforce its use. Install adequate fire alarm and suppression systems. Hold regular safety drills and update response plans accordingly. Designate experienced safety coordinators to identify hazards, enforce policies, and lead training.
Encourage staff to report concerns immediately without fear of blame or retaliation. A strong safety culture guided by comprehensive policies prevents injuries that lead to production delays, legal liabilities, and higher insurance costs.
Foster Employee Wellbeing
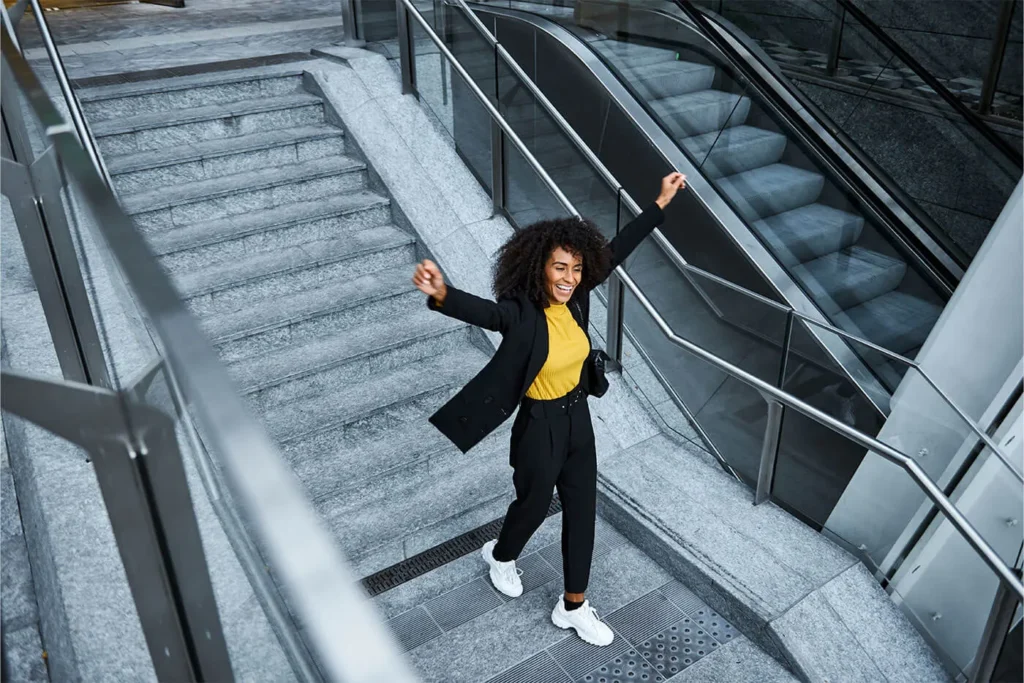
The most efficient workplaces actively support employees’ overall health and well-being. Provide an onsite health clinic offering medical care, physical therapy, and ergonomic assessments. Facilitate access to mental health services to help ease stress and anxiety.
Promote healthy lifestyles through nutrition guidance, gym subsidies, and smoking cessation support. Survey workers anonymously to identify wellbeing gaps needing improvement.
Accommodate disabilities and medical restrictions so valuable team members can continue contributing. Reward safe behavior and allow staff to take part in efficiency initiatives. An invested, supported workforce is key to maximizing sustainable productivity.
Promote Collaboration and Communication
Efficiency improves when employees feel connected to the team and understand how their role fits into larger goals. Encourage collaboration by designing open floor plans with gathering spaces. Arrange processes to facilitate interaction between departments. Provide projection screens for company-wide announcements and virtual meetings.
Use digital messaging boards to share real-time performance data, reminders, and motivation. Host all-hands meetings where staff can share ideas and recognize team members’ accomplishments. Train managers to actively listen, provide feedback, and keep teams aligned.
Make sure everyone understands quality standards, procedures, and objectives. Strong internal communication, transparency, and collaboration give workers purpose while tapping collective wisdom to continuously improve. An engaged, invested team propels sustainable gains in efficiency.
Ensuring Compliance: Navigating Efficiency Laws in the Industrial Setting
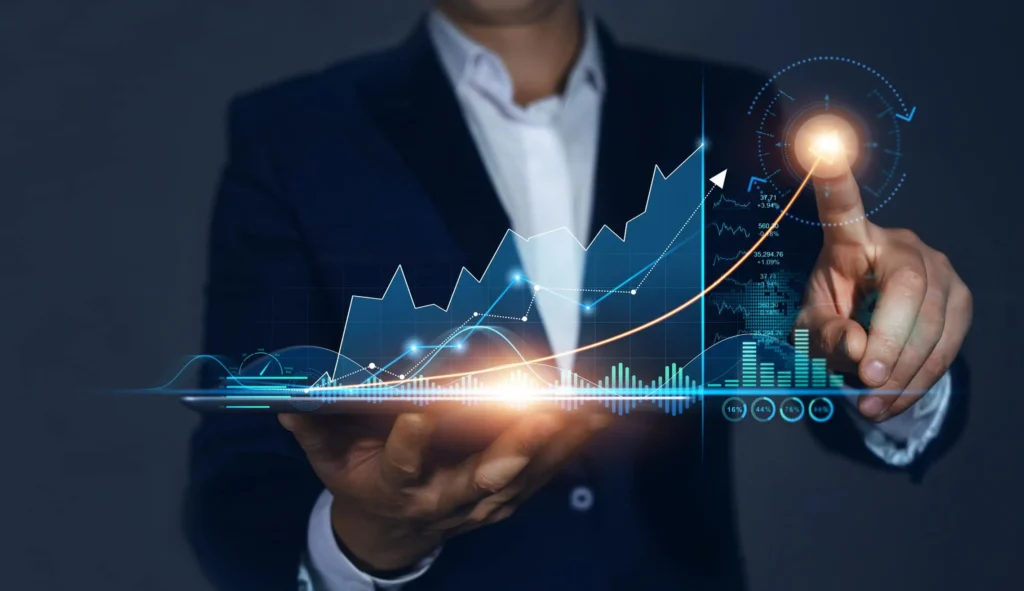
Efficiency in the industrial sector not only hinges on optimizing workplace conditions but also requires adherence to relevant efficiency laws.
These laws are crucial for safeguarding both the workforce and the company itself. This section delves into the importance of understanding and complying with efficiency laws in industrial settings.
Navigating Compliance:
Efficiency laws encompass a spectrum of regulations aimed at promoting a safe, fair, and productive working environment. From occupational safety standards to environmental regulations, industries must navigate these legal frameworks to ensure seamless operations.
Compliance involves not only meeting minimum requirements but also staying abreast of updates and changes in legislation.
Companies that proactively integrate legal considerations into their operations demonstrate a commitment to responsible and sustainable practices.
Challenges and Solutions:
Navigating efficiency laws can pose challenges, especially in dynamic regulatory landscapes. Companies may face complexities in interpreting and implementing regulations effectively.
To address this, investing in legal counsel and staying engaged with industry associations can provide valuable insights. Moreover, fostering a culture of compliance within the organization, where employees are educated on relevant laws and regulations, can serve as a proactive measure.
By viewing compliance not as a hindrance but as a strategic imperative, companies can navigate legal complexities more effectively.
Conclusion
Optimizing the workplace environment in terms of lighting, noise, ergonomics, air quality, safety, and well-being initiatives allows industrial facilities to operate at peak efficiency.
When employees can work comfortably, safely, and collaboratively within thoughtfully designed workspaces, they perform to their full potential with minimal errors, incidents, or disruptions.
The initial investments needed to enhance working conditions pay for themselves over time through increased productivity, better morale, reduced healthcare costs, and avoidance of safety fines. Making the work environment a strategic priority means manufacturers can gain a true competitive edge.